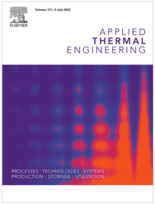
Résumé
Integrating Compressed Air Energy Storage (CAES) to a variable and unsteady energy source can help provide a levelized power output. This is particularly attractive for off-shore wind turbines integrated with the energy storage that has high efficiency. Such efficiency is possible if the compression portion can be isothermal, and a novel approach has been developed to achieve this by employing water spray during compression to promote heat transfer. This concept has been previously investigated with one-dimensional simulations that indicated spray cooling with droplet heat transfer over a large total surface area allows high-efficiency compression. However, the actual application is more complicated, and therefore the present study examines this concept with detailed two-dimensional unsteady flow simulations. In particular, multi-phase computational fluid dynamics is implemented in an axisymmetric domain to investigate compression in a cylinder for first-stage and second-stage compression using a spray discharge within the cylinder at various mass loadings. The spray is based on a single pressure-swirl nozzle directed along the centerline and operating at the maximum liquid mass flux possible while retaining a mean droplet diameter of no more than 30 µm. The two-dimensional simulations uncovered flow characteristics such as vortex formation for the air-flow near the cylinder head and strong spatial variations in droplet size and concentration. Despite these effects, the overall two-dimensional efficiency was similar to that of one-dimensional predictions. The results also indicated that a single pressure-swirl nozzle injection resulted in an injected mass loading of 1.6 and yielded efficiency as high as 93% for a first-stage compression cycle. However, a second-stage compression cycle (with an intake pressure of 10 bar) using this same single nozzle resulted in reduced overall work efficiency indicating that a multi-nozzle configuration should be considered.
Détails
- Titre original : Simulation of spray direct injection for compressed air energy storage.
- Identifiant de la fiche : 30016764
- Langues : Anglais
- Source : Applied Thermal Engineering - vol. 95
- Date d'édition : 25/02/2016
- DOI : http://dx.doi.org/10.1016/j.applthermaleng.2015.11.008
Liens
Voir d'autres articles du même numéro (37)
Voir la source
Indexation
-
Simulation of exhaust gas heat recovery from a ...
- Auteurs : GOLMAN B., JULKLANG W.
- Date : 12/2014
- Langues : Anglais
- Source : Applied Thermal Engineering - vol. 73 - n. 1
Voir la fiche
-
Research on LiBr-H2O absorption refrigeration s...
- Auteurs : YANG Q., ZHANG X., SHI W., et al.
- Date : 06/04/2011
- Langues : Anglais
- Source : Sources/sinks Alternative to the Outside Air for Heat Pump and Air-conditioning Techniques (Alternative Sources - AS), Padua, Italy, April 5-7, 2011. / International Sorption Heat Pump Conference (ISHPC11), Padua, Italy, April 6-8, 2011.
- Formats : PDF
Voir la fiche
-
Performance of solar sorption cooling systems w...
- Auteurs : HAGEL K., HELM M., SCHWEIGLER C.
- Date : 21/08/2011
- Langues : Anglais
- Source : Proceedings of the 23rd IIR International Congress of Refrigeration: Prague, Czech Republic, August 21-26, 2011. Overarching theme: Refrigeration for Sustainable Development.
- Formats : PDF
Voir la fiche
-
Etude numérique de la solidification de l'eau a...
- Auteurs : SASAGUCHI K., KUSANO K.
- Date : 1995
- Langues : Japonais
- Source : Trans. JAR - vol. 12 - n. 3
Voir la fiche
-
Electrospray cooling for microelectronics.
- Auteurs : DENG W., GOMEZ A.
- Date : 05/2011
- Langues : Anglais
- Source : International Journal of Heat and Mass Transfer - vol. 54 - n. 11-12
Voir la fiche